Operations
We have with us the most modern and finest machinery available in the world. We have provided the best of infrastructure to ensure quality. Our manufacturing operations are vertically integrated to facilitate all the process under one roof. Each of our operations is executed with up -to-date machinery and equipment
Zero Liquid Discharge
We are the 1st company in Tirpur to have setup such a plant.
It means zero discharge of wastewater from Industries. A ZLD system involves a range of advanced wastewater treatment technologies to recycle, recovery and re-use of the ‘treated’ wastewater and thereby ensure there is no discharge of wastewater to the environment. A typical ZLD system comprises of the following components:
- Pre-treatment
- Reverse Osmosis
- Evaporator & Crystallizer
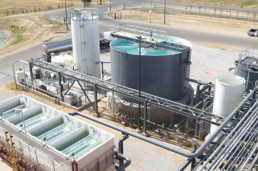

NEED FOR ZLD
Most polluting industries such as Pharma, Pulp & Paper, Tanneries, Textile Dyeing, Chemicals , Power Plants etc generate wastewater with high salinity/TDS. Discharge of saline but treated wastewater pollutes ground and surface waters. Several states in India including Tamil Nadu are water stressed. Competing demands for water from agriculture and domestic use has limited industrial growth. TN has taken a lead on ZLD due to absence of fully flowing perennial river. Most rivers originate from neighboring states and water sharing is enmeshed in disputes. Several landmark pollution cases and court battles have hastened this, such as the Vellore and Tirupur court cases. Other states such as Gujarat and Karnataka also are now are considering ZLD.
BENEFITS OF ZLD
The project for ZLD is perhaps the first of its kind in the world. Key benefits of the project are:
- Recycling >98% of the water
- Reuse of > 90% of the salt
- Cleaning of the local environment
To save costs and reduce the capacity needed, comprehensive water audits are usually performed which also ensure that the system deals only with the most polluting streams. Installing ZLD technology is therefore often beneficial for the plant’s water management; encouraging close monitoring of water usage, avoiding wastage and promotes recycling by conventional and far less expensive solutions. High operating costs can be justified by high recovery of water (>90- 95%) and recovering of several by products from the salt. A more sustainable growth of the industry while meeting most stringent regulatory norms. Possibility of use of sewage for recovery of water, for Industrial and municipal use, using ZLD technologies. Reduction in water demand from the Industry frees up water for Agriculture and Domestic demands.
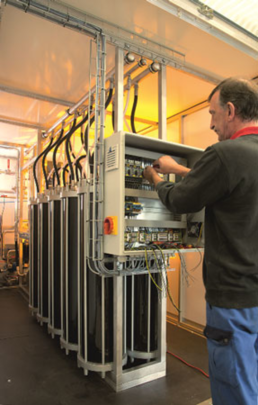
Knitting
Our Knitting Plants have 34 state of the art knitting machines both “Circular” and “Flat” knitting machines – Mayer & Cie, Terrot (Germany), Smart(Taiwan), Kough Hung (Taiwan),Flying Tiger (Taiwan)
Terrot Machineries
-
- Single and Double Jersey
- Rib,Interlock
- AutoStripes
Capacity: 3 tonnes/day
Terrot Machineries
- Double Jersy
- Flatback
- Drop Needle
- Waffle
- Stripes
- Durby
Capacity: 2 tonnes/day
Mayer & Cie Machines
- Jacquard Single Jersey
- Jacquard Double Jersy
- AutoStripes
- Interlock
Capacity: 1 tonnes/day
Flying Tiger Machines
- Jacquard Collar
- Stripes
Capacity: 3,000 Sets Per/day
Gassing
Gassing to a finish where cotton thread is passed through a flame at high speed to reduce its fuzz and have a greater sheen. Gassing is done in a wrap form prior to mercerizing and dyeing Machinery available for Gassing.
Machinery : Metler,Italy
Capacity: 3 tonnes/day
Yarn Mercerizing
Continues mercerizing for tubular knitted fabrics, free from wrinkles and grease lines uniform mercerization without edge mark 30-40% saving dyes and chemicals. International mercerizing excellent silky effect and brightness fastest delivery at reasonable time.
Machinery: JAGELLU, Italy
Capacity: 1.5 tonnes/day
Fabric Mercerizing
Machinery: MCS Italy
Capacity: 1.5 tonnes/day
Fabric Dyeing
We use the latest soft flow dyeing machines which maintains a consistent shade through out the fabric.
Machinery: KROMSON RANGES, TURKEY
Capacity:1050,650,450,200,150,75 and 25 Kgs
Yarn Dyeing
Machinery: The world’s best range of OBEM Lorris Bellini of Italy for Cone and Hank dyeing
Capacity: :500kg,300kg ,75kg,25kg in cone and 300kg,200kg,100kg and 25kg for Hangs
Relax Dryer
Relax dryer for tension less drying
Machinery: R.F Dryer-SWA
Capacity: 1500Kgs/day
Compacting
Shrinkage control or compacting is a mechanical shrinkage control process which is achieved by the compacting machine imported from TUBE-TEXUSA. It maintains the shrinkage control to below 5% meeting all international standards
Machinery : Ssango, Korea
Capacity : 4 Tonnes / Day C
Garment Dyeing
We do garment dyeing, enzyme washing and chemical wash as per the market requirement
Garment Dyeing(Pigment Dyeing)
- Bio Wash
- Bio Polishing
- Anti-Pilling
- Sand Wash
- Golf Ball Wash
- Enzyme Wash
- Vintage Wash
- Acid Wash/Ozone
- Magic Wash
- Distress Finish
This is the latest range for soft hand feel without much pilling
Testing Lab
Testing lab is equipped with auto dispensing system and orientex’s color matching computer.
This enables to get exact matching in the needed source of light and without metamerism.
Computerized Auto Dispensing system enables to attain first time right shade to match buyer’s Requirement’s
Machinery: Orientex’s color matching computer
Embroidery
The fabric, cut fabric, semi stitched, fully stitched are embroidered according to pattern. Be it logo, chest and label, they can be embroidered in the inhouse Embroidery machine – TAJIMA – JAPAN
Machinery: Tajma – Japan
- Model: 6178
- Head: 20
- Color: 9 With Sequence
- Capacity : 4000 Pcs/Day
Printing
The process of applying colourants to the specific areas to produce a design Machinery available for Printing
Machinery :12 color rotary printing for pigment, discharge and reactive.
Capacity : 5 tonnes/day
Pattern Making
A pattern can be defined as a model or a replica of the various components pf a garment. It can be made of paper or plastic. Normally papers are used to make the patterns which are cheaper than plastic or other materials. In industries, they are using thick paper or card board instead of tissue paper for frequent applications.
- Importance of Pattern Making
- Patterns are acting as a time saving device
- We can preserve the patterns and use them whenever we want
- Patterns are very useful for “ Pattern Grading” process
- Using pattern grading process, we can Enlarge or reduce the base pattern from one size to Another size
Production
Total Area: 1,00,000 sq feet
Total Machinery:820
Manufacturing Capacity:
3 Button Polo: 9000 dozen/ month
Other styles:10000 dozen/month